Over the last decade, the ultraviolet (UV) LED market has grown substantially. Since 2008, there has been more than a fivefold increase in the number of companies manufacturing UV LEDs. Last year, we reviewed the current state of UV LED technology; a lot has changed since then, and UV LED adoption continues to accelerate. Much of this growth is due to the growing adoption of UVA LEDs in UV curing applications. The performance of UV LEDs, especially at UVA wavelengths, is improving, and LEDs are becoming more abundant and easier to source. The market is predicted to expand even more, as UVB and UVC LEDs improve in response to growing demand from emerging UV disinfection markets.

At conferences like SPIE Photonics West and the IUVA World Congress, new UV LED-driven applications, such as in-line water sterilization for homes and surface disinfection using a smartphone light, were discussed. However, while these new applications may soon be achievable, it is worthwhile to look at the current state of UV LED technology to evaluate its commercial viability. When evaluating UV LEDs for your system, you need to consider a few factors, such as:
- What peak wavelengths of LEDs are available in the UVA, UVB, and UVC regions?
- What is the output power of these LEDs?
- How efficient are these UV LEDs at the various wavelengths?
- What LED products and wavelengths are commercially available by manufacturer?
- Are UV LEDs viable alternatives to traditional UV light sources?
- What is the useable life of a UVC LED?
This article seeks to answer some of these questions, as well as provides an overview of the current state of UV LED technology and some of the technical barriers that are preventing UV LED advancements. We also created a downloadable database that provides an overview of the current UV LED product offerings available and their performance specs.
What are the Current Performance Limits of UV LED Technology?
Depending on your application, you will have different performance specifications for your UV light source. Many applications require a targeted peak wavelength for optimal performance, but some have even more stringent limitations on the light output. For example, phototherapy applications need to apply UVA, UVB, or a combination of these wavelengths to a patient’s skin without exposing them to any harmful UVC wavelengths. In other instances, you might need a specific power output for your application. UV curing systems, for example, require constant and intense light to ensure fast processing times, and almost all applications can benefit from increased efficiency as it will reduce operating costs and energy requirements.
So how do UV LEDs perform with respect to these parameters? The figure below shows a snapshot of the wavelengths, power or radiant flux, and efficiencies of commercially available LEDs. You can find a diode with virtually any peak wavelength between 240 nm and 400 nm. Some key wavelengths, such as 265 nm, 280 nm, 310 nm, and 365 nm, have options available from multiple manufacturers. However, the power and efficiency will depend significantly on the LED’s peak wavelength.
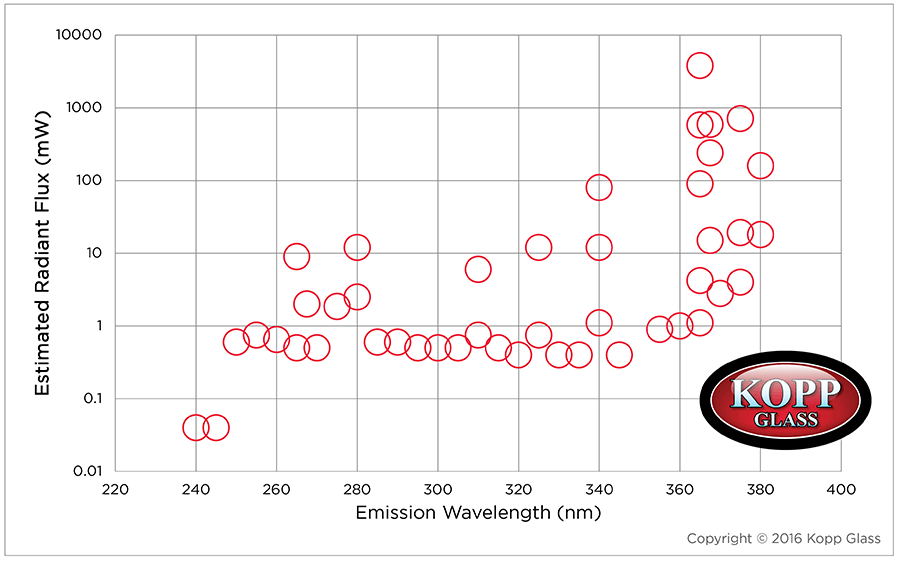
UVA LEDs (320 nm – 400 nm)
The most commercially viable UV LEDs are those that emit at UVA wavelengths. There are more than 30 UVA LEDs available, including models from companies such as SETi and Epigap LED. Their peak wavelengths range from 320 nm to 400 nm, with LEDs available at every 5 nm increment. However, the majority of available LEDs are centered around 360 to 380 nm. UVA LEDs have the highest efficiencies, with some approaching the efficiency of blue LEDs. UVA LEDs also have the largest available radiant flux or output power, ranging from 1 mW to 4000 mW, depending on the driving current.
The high efficiency and increased power output of UVA LEDs compared to UVB and UVC LEDs is partly due to the inherent properties of the substrate material. Generally speaking, UV LEDs use gallium nitride (GaN) or aluminum gallium nitride (AlGaN) layers to emit UV wavelengths. For the materials that emit UVA wavelengths, companies can grow the layers on sapphire substrates, GaN substrates, or sapphire with a buffer layer of GaN. For these materials, there is less of a lattice mismatch between emitter and substrate, which results in fewer defects and therefore higher efficiency and output. It also helps that visible LED manufacturers such as Philips and Nichia, have jumped into the UV LED game, bringing with them research expertise and best practices from their creation of short wavelength blue LEDs.
UVB LEDs (280 nm – 315 nm)
UVB LEDs are also commercially available but currently are less efficient and powerful than UVA LEDs. There are more than 20 UVB LEDs on the market, with peak wavelengths ranging from 280 nm to 315 nm. For the most part, the available power outputs are below 2 mW. One LED option with increased optical power output is manufactured by Dowa; this 280 nm LED achieves a radiant flux of 9 mW when driven at a forward current of 80 mA.
Again, the main driving factor in the lower output power and efficiency of UVB LEDs is the mismatch between emitting material and substrate material. It is common to see an LED with a sapphire substrate covered by an AlN or AlGaN buffer layer. While this configuration allows for the generation of UVB and UVC wavelengths, it has a higher defect density which results in reduced light extraction and efficiency. UV LED research presented at SPIE Photonics West addressed the defect densities of AlN and AlGaN sublayers (technical presentations 9748-29, 9748-54, 9748-57). Researchers are exploring various manufacturing processes to gain better light extraction; for instance, some are increasing the pressure applied to a sublayer as it grows to prevent defects from forming while others are altering the geometry of the sublayer surfaces to limit the number of defects. However, it is not clear that AlN or AlGaN sublayers will allow for the efficiency and power increases that are necessary for UV LEDs to match the performance of visible LEDs.
UVC LEDs (240 nm – 280 nm)
There are a large number of UVC LEDs available on the market, but much like UVB LEDs, their outputs and efficiencies remain low at this time. There are more than 20 UVC LEDs available at 5 nm increments between 240 nm and 280 nm. UVC LEDs have the lowest efficiency, and for most, the output power is less than 1 mW. There are some options for UVC LEDs with larger flux; for example, Crystal IS produces 255 nm, 265 nm, and 275 nm LEDs that, when driven at a high forward current, have a radiant flux of 8 mW or greater.
The limitations of UVC LEDs again stem from the limitations of the substrate and sublayer materials. However, it is expected that this wavelength region will receive the most focus from LED manufacturers, due to the demand for an environmentally friendly, reliable, and energy efficient light source for sterilization and disinfection applications. As the Yole Développement market research report predicted, UVC LEDs are improving quickly, and industry experts believe that within the next five years, the power output of UVC LEDs could reach 100mW while the efficiency and lifetime could match those of currently available UVA LEDs. However, at these low UV wavelengths, encapsulate transmission, degradation, and lifetime remains a major limitation.
Available UV LED Product Database
UV LED technology is rapidly evolving, and with more than 20 LED manufacturers and 80 different UV LED products, it can be difficult to determine the best product available on the market. To make the selection process easier, we reviewed these UV LED manufacturers and their products and created a tool that lists the wavelengths available from each manufacturer based on their available production information. Download our database to gain an understanding of the current UV LED product offerings, and to learn what UV LEDs are available for your application.
There are many reasons why you should choose to use UV LEDs when designing a product. However, when selecting an appropriate LED, some of the most important factors to consider are the power, efficiency, wavelength, and cost of the LED. At the moment, UVA LEDs show the most commercial viability. Many UV curing manufacturers are successfully using LEDs within this wavelength range in their new devices and equipment. However, for UVB and UVC LEDs to realize widespread adoption into existing applications, further improvements to their efficiency, power outputs, and price will be necessary.