Glass is an immensely versatile material; it is used every day in numerous applications, many that most of us are not even aware of. We use it to drink beverages, to store food, and as windows in our homes and automobiles but glass is also used in many unseen applications. For instance, glass components are used in medical diagnostic equipment, electronics, building insulation, and as a reinforcement material in things like surf boards, wind turbines, and orthopedic casts. Every day we interact with a myriad of glass forms and compositions.
So What Is Glass?
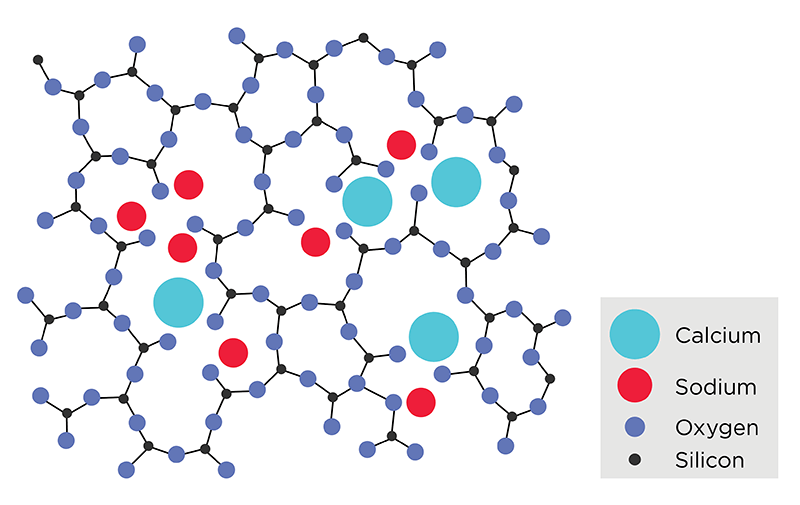
Note: In this 2D representation, the additional silica bond to oxygen is not visible but would be present in a 3D model.
Glass is an amorphous material that lacks a long range periodic crystalline structure. Glasses can be formed through several methods but the most common method involves heating raw materials into a molten liquid and then rapidly cooling the liquid in such a way that the atoms remain in a randomly arranged atomic state.
When using the melting/cooling method to form glass, the process often begins as a mixture of several critical raw material powders. These powder mixtures are composed of many different components, with each playing an important role. In most glasses, the compositions are engineered to include network formers, fluxing agents, property modifiers, fining agents, and colorants. The chemical formulation dictates the physical properties and characteristics of the formed glass.
These raw materials are then heated to a sufficient melting temperature so that a homogeneous viscous liquid is formed. At this point, depending on the manufacturing technique, the molten glass can be manipulated and shaped into the desired glass form. The chemical formulation can be altered to meet different performance specifications or to improve manufacturability.
3 Most Common Commercial Glass Types and Their Applications
Glass compositions are engineered to exhibit different physical, chemical, and optical properties. Different applications demand specific types of glass and manufacturing processes. In commercial glass manufacturing, several glass compositions are commonly used. We’ll briefly highlight three of the most common commercial glass compositions, their properties, and typical applications.
Glass Type | Primary Components | Linear Thermal Expansion | Thermal Shock Resistance | Chemical Resistance | Applications |
---|---|---|---|---|---|
Borosilicate | SiO2, B2O3 | -30-60 x 10-7/°C | Average - High | High |
|
Soda-lime silicate | SiO2, Na2O, CaO | -80-100 x 10-7/°C | Low | Average |
|
Phosphates | P2O5 | -90-110 x 10-7/°C | Low | Low, except high resistance to hydrofluoric acid |
|
Soda-lime Silica Glasses
Open a refrigerator and take a look at the containers and jars within, most likely they are made with soda-lime silica glass. This family of glasses encompasses many of the glass compositions used to create food and beverage containers, decorative tableware and accessories, and windows. Soda-lime silica glass compositions account for nearly 90% of the glass manufactured in the world.
Its prevalence is due to the fact that it’s relatively inexpensive to manufacture; the materials are common and when combined, they can be melted at a lower temperature than many other glass compositions. Also, the manufacturing processes have been refined, optimized, and automated over the last century to improve through-put for mass production of these glasses.
However, soda-lime silica glasses are typically not as durable as other glasses, including borosilicate compositions. They tend to be prone to thermal shock failure and can degrade in chemically corrosive environments. However, through additional manufacturing like chemical and thermal strengthening, the durability and strength can be improved.
Borosilicate Glasses
In harsh, demanding applications, borosilicate glasses are commonly used for their superior durability. They have good thermal shock resistance and can withstand extreme thermal cycling with minimal effect. For instance, Pyrex, a commercial borosilicate composition created by Corning, Inc., is commonly used for baking at home or performing experiments in the lab. It can go from cooking in the oven to air cooling on the counter without damage. This is due to the low coefficient of thermal expansion which allows the glass to develop fewer internal stresses during the heating and cooling processes that cause cracking or breaking.
While many materials may quickly degrade in abrasive environments, borosilicate compositions have shown an ability to stand up to the task. They are commonly used in lighting applications where surface degradation and loss of transmitted light are undesirable.
In industrial or transportation environments, glass is frequently exposed to harsh chemicals like jet fuel, hydraulic fluid, acids, photoinitiators, saline solutions, and petroleum products. Even persistent exposure to water can cause damage to some glasses. Borosilicate glasses have shown an ability to resist both moisture and chemical attack and will continue to perform as expected despite long exposures to water and chemicals. Because of this, these glass compositions are commonly used for laboratory glassware, sight glass within industrial equipment, transformer bushings, explosion-proof lighting, and exterior aircraft lenses.
Phosphate Glasses
Phosphate glasses are mainly composed of the network former P2O5 where the previously mentioned glasses use SiO2 or B2O3 as the primary glass network formers. These glasses feature a high resistance to hydrofluoric acid, but otherwise they have a relatively low resistance to chemical corrosion. The compositions can be made more resistant to the chemicals and the environment by engineering the composition for the specific applications.
Phosphate glasses are well suited for doping with various colorants, including transition metal ions and rare earth oxides. This ability results in glasses that exhibit unique and desirable transmission spectrum. These colored glasses have found their niche in various medical, military, and scientific applications. Bioactive glass, which is the material of choice to promote bone growth in the medical industry, is also a phosphate based glass composition.
Choosing a Glass
At first glance, it may seem difficult to decide which glass is best for a specific application. Is it more important to have high thermal shock resistance or chemical resistance? There isn’t necessarily a black or white answer. It depends on the environment the glass will be exposed to as well as the performance specifications required. Once the desired performance specifications are known, a review of the glass’ optical, thermal, chemical, and mechanical properties will determine what glass would perform the best and be the most economic.
Learn More About Glass
Glass is a unique and complex material–much different than other transparent materials. If you’re new to designing glass lenses or components, it can be an intimidating challenge.
To help you design better-performing glasses lenses, we created a comprehensive eBook that includes more than 40 pages of information on the thermal, optical, and mechanical properties of glass.
If you want to learn how to design glass lenses and components that are optimized for both your performance requirements and operating environment, download our free eBook.